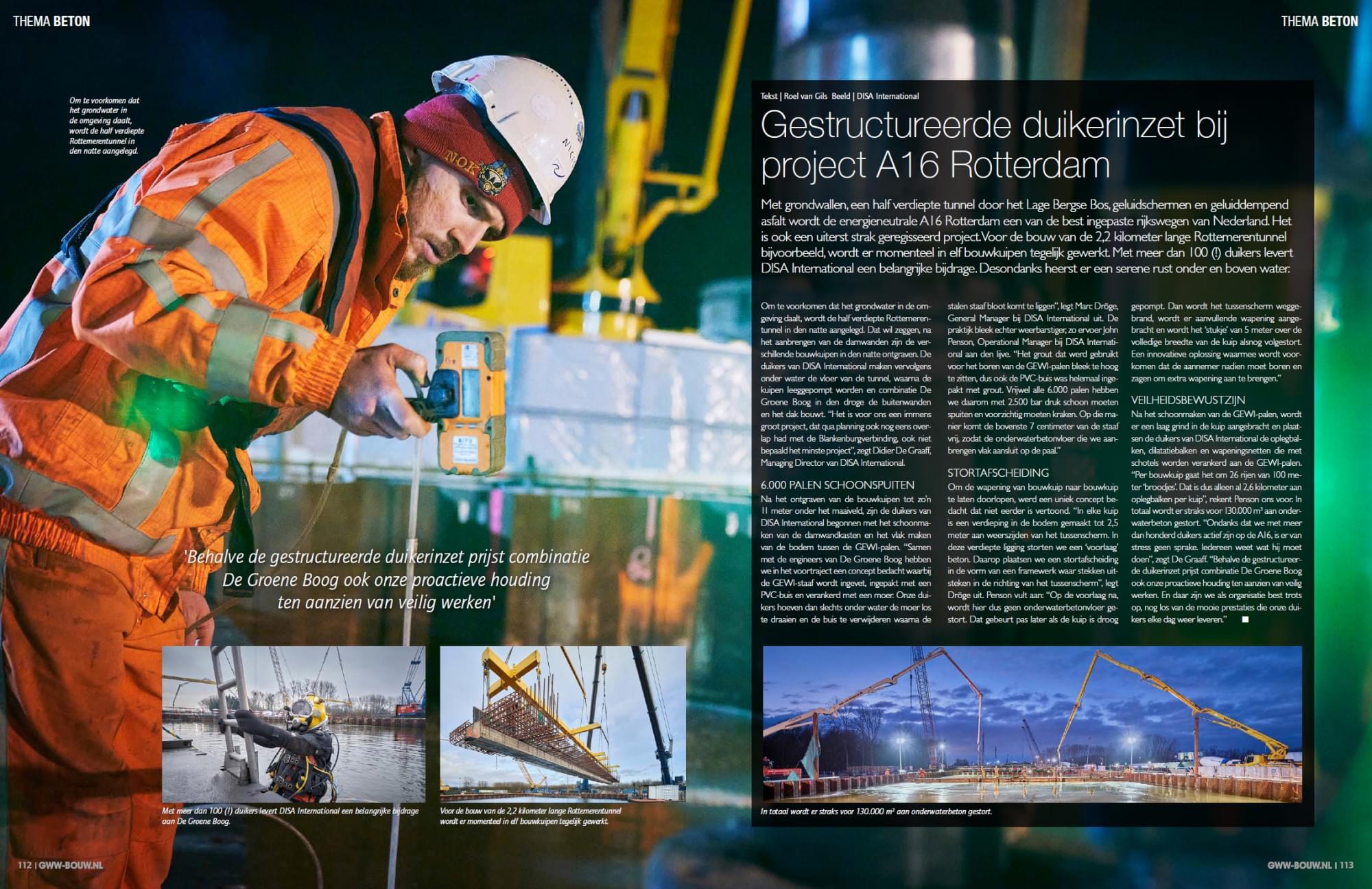
STRUCTURED DEPLOYMENT OF DIVERS ON A16
Published on: 22/09/2022
STRUCTURED DEPLOYMENT OF DIVERS ON A16 :
With embankments, a semi-sunken tunnel through the Lage Bergse Bos, noise barriers and noise dampening, the energy-neutral A16 Rotterdam will be one of the best integrated motorways in the Netherlands. It is also an extremely tightly managed project. For the construction of the 2,2 kilometre-long Rottemerentunnel, for example, eleven construction sites are currently under construction. Work is currently being carried out in eleven pits simultaneously. With more than 100 (!) divers, DISA International is making a major contribution. Despite this, there is a serene calm under and above water.
In order to prevent lowering of the groundwater in the area, the Rottemerentunnel will be constructed in first instance in the wet. After installation of the sheet piles, the different construction pits were excavated. DISA divers then constructed the floor of the tunnel underwater, after which the pits are pumped empty and the combination De Groene Boog continues in the dry the building of the outer wall and the roofstructure. "It is an immensely large project for us, and its planning also overlapped with the Blankenburg connection project, which is not exactly the least of all projects," says Didier De Graaff, Managing Director of DISA International.
CLEANING 6,000 PILES
After excavating the construction pits to around 11 metres below ground level, DISA divers began by cleaning the sheet piles and levelling the soil between the GEWI piles. "Along with the engineers of De Groene Boog, we devised a concept in the preliminary phase whereby the GEWI were greased, encased in a PVC pipe and anchored with a nut. Our divers then had to unscrew the nut and remove the PVC underwater, after which the steel bar became exposed," explains Marc Dröge, General Manager at DISA Civil Construction. The practice, however, proved to be more difficult, says John Penson, Operational Manager at DISA Civil Construction. "The grout used for drilling the GEWI piles turned out to be of high denisty, so the PVC pipe was also completely encased in grout. We therefore drilled almost all 6,000 piles We therefore had to clean the piles with 2,500 bar pressure and carefully cracked them. That way, the top 7 centimetres of the pile were cleared, so that the underwater concrete floor could fit flush to the pile.
STORM SEPARATION
To allow the reinforcement to run through the cofferdam , a unique concept was devised. "In each cofferdam, a floor has been created up to 2.5 metres on and either side from the intermediate seperation screen. In this location we poured a 'pre-laid layer' of concrete. On top of this, a bulkhead in the form of a framework with reinforcement protruding out of it in the direction of the intermediate screen", explains Dröge. Penson adds: "Apart from the pre-laid layer, no underwater concrete floor was required to be poured here. That will only be performed in a later stage when the building pit is dry and the intermediate screen is removed. Additional reinforcement are applied over these 5-metres across the full width and than filled with concerete. An innovative solution that prevents the contractor from having to drill and saw for extra reinforcement afterwards.
SAFETY AWARENESS
After cleaning the GEWI piles, a layer of gravel is installed in the pit and the divers place the overlay beams, dilatation beams and reinforcement nets these are anchored to the piles using floats. "Each cofferdam involves 26 rows of 100-metre'. That's 2.6 kilometres of piled beams per cofferdam Penson calculated. In total, 130,000 m3 of underwater concrete will soon be poured. "Despite the fact that we have more than a hundred divers working on the A16, there is no stress. Everyone knows what there task is", says De Graaff. "Apart from the structured deployment of the divers, the Groene Boog consortium praised our proactive attitude towards safe working. And we are quite proud of that our organisation, even apart from the excellent performance that our divers deliver every day.